Tehnologia de decupare a napolitanelor, ca etapă critică în procesul de fabricație a semiconductorilor, este direct legată de performanța, randamentul și costurile de producție ale cipurilor.
#01 Contextul și semnificația tăierii în cuburi de napolitane
1.1 Definiția tăierii în cuburi a napolitanelor
Tăierea în cuburi a napolitanelor (cunoscută și sub denumirea de scribing) este o etapă esențială în fabricarea semiconductorilor, având ca scop împărțirea napolitanelor procesate în mai multe matrițe individuale. Aceste matrițe conțin de obicei funcționalitatea completă a circuitului și sunt componentele de bază utilizate în cele din urmă în producția de dispozitive electronice. Pe măsură ce designul cipurilor devin mai complex, iar dimensiunile continuă să se micșoreze, cerințele de precizie și eficiență pentru tehnologia de tăiere în cuburi a napolitanelor devin din ce în ce mai stricte.
În operațiunile practice, tăierea napolitanelor utilizează de obicei unelte de înaltă precizie, cum ar fi lamele diamantate, pentru a asigura că fiecare matriță rămâne intactă și complet funcțională. Etapele cheie includ pregătirea înainte de tăiere, controlul precis în timpul procesului de tăiere și inspecția calității după tăiere.
Înainte de tăiere, placheta trebuie marcată și poziționată pentru a asigura traiectorii precise de tăiere. În timpul tăierii, parametri precum presiunea sculei și viteza trebuie controlați cu strictețe pentru a preveni deteriorarea plachetei. După tăiere, se efectuează inspecții complete ale calității pentru a se asigura că fiecare cip îndeplinește standardele de performanță.
Principiile fundamentale ale tehnologiei de tăiere a napolitanelor cuprind nu doar selecția echipamentului de tăiere și setarea parametrilor procesului, ci și influența proprietăților mecanice și a caracteristicilor materialelor asupra calității tăierii. De exemplu, napolitanele de siliciu dielectric cu k scăzut, datorită proprietăților lor mecanice inferioare, sunt foarte susceptibile la concentrarea stresului în timpul tăierii, ceea ce duce la defecțiuni precum ciobirea și fisurarea. Duritatea și fragilitatea reduse ale materialelor cu k scăzut le fac mai predispuse la deteriorarea structurală sub forță mecanică sau stres termic, în special în timpul tăierii. Contactul dintre sculă și suprafața napolitanei, împreună cu temperaturile ridicate, pot exacerba și mai mult concentrarea stresului.
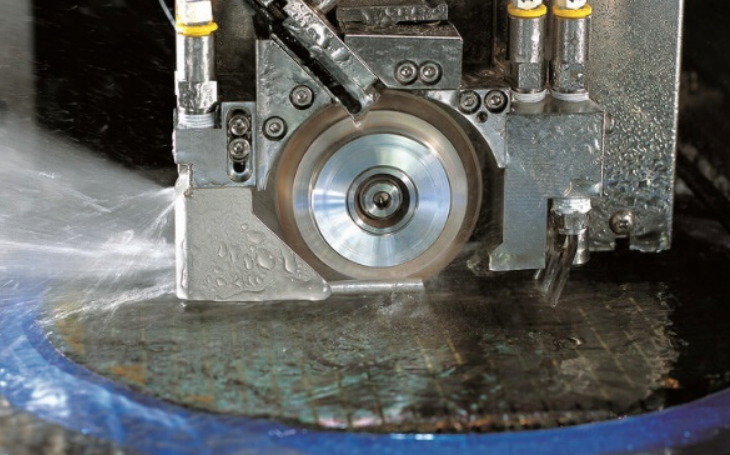
Odată cu progresele înregistrate în știința materialelor, tehnologia de tăiere a plachetelor s-a extins dincolo de semiconductorii tradiționali pe bază de siliciu pentru a include materiale noi, cum ar fi nitrura de galiu (GaN). Aceste materiale noi, datorită durității și proprietăților lor structurale, prezintă noi provocări pentru procesele de tăiere, necesitând îmbunătățiri suplimentare ale uneltelor și tehnicilor de tăiere.
Fiind un proces critic în industria semiconductorilor, tăierea în cuburi a plachetelor continuă să fie optimizată ca răspuns la cerințele în continuă evoluție și la progresele tehnologice, punând bazele viitoarelor tehnologii de microelectronică și circuite integrate.
Îmbunătățirile tehnologiei de tăiere a napolitanelor merg dincolo de dezvoltarea de materiale și unelte auxiliare. Acestea includ, de asemenea, optimizarea proceselor, îmbunătățirea performanței echipamentelor și controlul precis al parametrilor de tăiere. Aceste progrese vizează asigurarea unei precizii, eficienței și stabilității ridicate în procesul de tăiere a napolitanelor, satisfăcând nevoia industriei semiconductorilor de dimensiuni mai mici, o integrare mai mare și structuri de cipuri mai complexe.
Zona de îmbunătățire | Măsuri specifice | Efecte |
Optimizarea proceselor | - Îmbunătățirea pregătirilor inițiale, cum ar fi poziționarea mai precisă a plachetelor și planificarea traseului. | - Reduce erorile de tăiere și îmbunătățește stabilitatea. |
- Minimizează erorile de tăiere și îmbunătățește stabilitatea. | - Adoptă mecanisme de monitorizare și feedback în timp real pentru a regla presiunea, viteza și temperatura sculei. | |
- Rate mai mici de spargere a plachetelor și îmbunătățirea calității cipurilor. | ||
Îmbunătățirea performanței echipamentelor | - Utilizați sisteme mecanice de înaltă precizie și tehnologii avansate de control automat. | - Îmbunătățește precizia de tăiere și reduce risipa de material. |
- Introducerea tehnologiei de tăiere cu laser potrivită pentru napolitane cu materiale cu duritate ridicată. | - Îmbunătățirea eficienței producției și reducerea erorilor manuale. | |
- Creșterea automatizării echipamentelor pentru monitorizare și ajustări automate. | ||
Control precis al parametrilor | - Reglați fin parametri precum adâncimea de așchiere, viteza, tipul sculei și metodele de răcire. | - Asigurarea integrității matriței și a performanței electrice. |
- Personalizați parametrii în funcție de materialul, grosimea și structura plăcii. | - Creșterea ratelor de randament, reducerea risipei de materiale și scăderea costurilor de producție. | |
Semnificație strategică | - Explorarea continuă a unor noi căi tehnologice, optimizarea proceselor și îmbunătățirea capacităților echipamentelor pentru a satisface cerințele pieței. | - Îmbunătățirea randamentului și a performanței de fabricație a cipurilor, sprijinind dezvoltarea de noi materiale și designuri avansate de cipuri. |
1.2 Importanța tăierii napolitanelor în cuburi
Tăierea cubulețelor napolitane joacă un rol esențial în procesul de fabricație a semiconductorilor, având un impact direct asupra etapelor ulterioare, precum și asupra calității și performanței produsului final. Importanța sa poate fi detaliată după cum urmează:
În primul rând, precizia și consecvența tăierii în cuburi sunt esențiale pentru asigurarea randamentului și fiabilității cipurilor. În timpul fabricației, napolitanele trec prin mai multe etape de procesare pentru a forma numeroase structuri de circuite complexe, care trebuie împărțite cu precizie în cipuri individuale (die-uri). Dacă există erori semnificative de aliniere sau tăiere în timpul procesului de tăiere în cuburi, circuitele pot fi deteriorate, afectând funcționalitatea și fiabilitatea cipului. Prin urmare, tehnologia de tăiere în cuburi de înaltă precizie nu numai că asigură integritatea fiecărui cip, dar previne și deteriorarea circuitelor interne, îmbunătățind rata generală de randament.
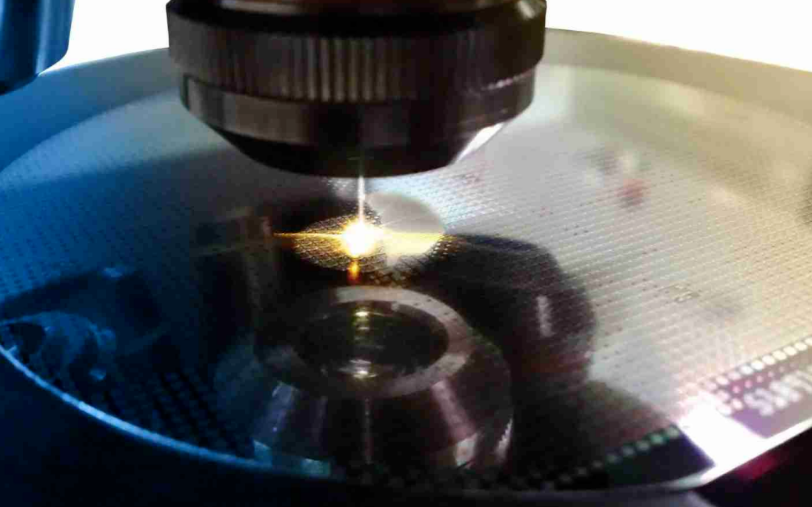
În al doilea rând, tăierea cubulețelor din napolitane are un impact semnificativ asupra eficienței producției și a controlului costurilor. Fiind o etapă crucială în procesul de fabricație, eficiența sa afectează direct progresul etapelor ulterioare. Prin optimizarea procesului de tăiere cubulețe, creșterea nivelului de automatizare și îmbunătățirea vitezei de tăiere, eficiența generală a producției poate fi mult îmbunătățită.
Pe de altă parte, risipa de material în timpul tăierii în cuburi este un factor critic în gestionarea costurilor. Utilizarea tehnologiilor avansate de tăiere în cuburi nu numai că reduce pierderile inutile de material în timpul procesului de tăiere, dar și crește utilizarea plachetelor, reducând astfel costurile de producție.
Odată cu progresele în tehnologia semiconductorilor, diametrele plachetelor continuă să crească, iar densitățile circuitelor cresc în consecință, ceea ce impune cerințe mai mari tehnologiei de tăiere în cuburi. Plachetele mai mari necesită un control mai precis al căilor de tăiere, în special în zonele cu circuite cu densitate mare, unde chiar și abateri minore pot face ca mai multe cipuri să se defecteze. În plus, plachetele mai mari implică mai multe linii de tăiere și etape de proces mai complexe, necesitând îmbunătățiri suplimentare ale preciziei, consecvenței și eficienței tehnologiilor de tăiere în cuburi pentru a face față acestor provocări.
1.3 Procesul de tăiere a napolitanelor
Procesul de tăiere a napolitanelor cuprinde toate etapele, de la faza de pregătire până la inspecția finală a calității, fiecare etapă fiind esențială pentru asigurarea calității și performanței cipurilor tăiate. Mai jos este o explicație detaliată a fiecărei faze.
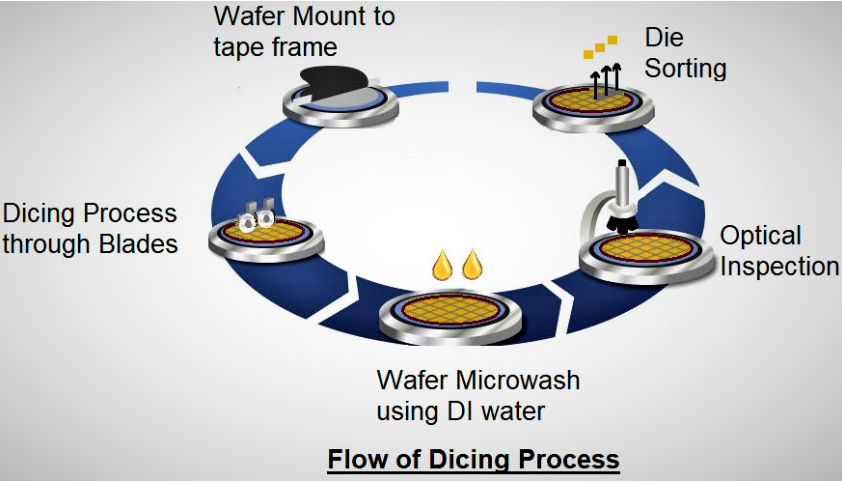
Fază | Descriere detaliată |
Faza de pregătire | -Curățarea napolitanelorFolosiți apă de înaltă puritate și agenți de curățare specializați, combinați cu frecare cu ultrasunete sau mecanică, pentru a îndepărta impuritățile, particulele și contaminanții, asigurând o suprafață curată. -Poziționare precisăUtilizați echipamente de înaltă precizie pentru a vă asigura că napolitana este împărțită cu precizie de-a lungul căilor de tăiere proiectate. -Fixarea napolitanelorFixați placheta pe un cadru cu bandă pentru a menține stabilitatea în timpul tăierii, prevenind deteriorarea cauzată de vibrații sau mișcare. |
Faza de tăiere | -Tăierea cu lamăFolosește lame diamantate rotative de mare viteză pentru tăiere fizică, potrivite pentru materiale pe bază de siliciu și eficiente din punct de vedere al costurilor. -Tăiere cu laserUtilizează fascicule laser de înaltă energie pentru tăiere fără contact, ideală pentru materiale fragile sau cu duritate ridicată, cum ar fi nitrura de galiu, oferind o precizie mai mare și o pierdere mai mică de material. -Noi tehnologiiIntroducerea tehnologiilor de tăiere cu laser și plasmă pentru a îmbunătăți și mai mult eficiența și precizia, reducând în același timp zonele afectate termic. |
Faza de curățare | - Folosiți apă deionizată (apă DI) și agenți de curățare specializați, combinați cu curățare cu ultrasunete sau prin pulverizare, pentru a îndepărta resturile și praful generate în timpul tăierii, împiedicând reziduurile să afecteze procesele ulterioare sau performanța electrică a așchiei. Apa deionizată de înaltă puritate evită introducerea de noi contaminanți, asigurând un mediu curat pentru napolitane. |
Faza de inspecție | -Inspecție opticăFolosiți sisteme de detectare optică combinate cu algoritmi de inteligență artificială pentru a identifica rapid defectele, asigurându-vă că nu apar fisuri sau ciobiri în așchiile tăiate cubulețe, îmbunătățind eficiența inspecției și reducând erorile umane. -Măsurarea dimensiunilorVerificați dacă dimensiunile cipului corespund specificațiilor de proiectare. -Testarea performanței electriceAsigurați-vă că performanța electrică a cipurilor critice respectă standardele, garantând fiabilitatea în aplicațiile ulterioare. |
Faza de sortare | - Folosiți brațe robotice sau ventuze pentru a separa așchiile calificate de cadrul benzii și a le sorta automat în funcție de performanță, asigurând eficiența și flexibilitatea producției, îmbunătățind în același timp precizia. |
Procesul de tăiere a plachetelor implică curățarea, poziționarea, tăierea, curățarea, inspecția și sortarea plachetelor, fiecare etapă fiind critică. Datorită progreselor în automatizare, tăiere cu laser și tehnologii de inspecție prin inteligență artificială, sistemele moderne de tăiere a plachetelor pot obține o precizie și o viteză mai mari și pierderi de material mai mici. În viitor, noile tehnologii de tăiere, cum ar fi laserul și plasma, vor înlocui treptat tăierea tradițională cu lame pentru a satisface nevoile unor designuri de cipuri din ce în ce mai complexe, impulsionând în continuare dezvoltarea proceselor de fabricație a semiconductorilor.
Tehnologia de tăiere a napolitanelor și principiile sale
Imaginea ilustrează trei tehnologii comune de tăiere a napolitanelor:Tăierea cu lamă,Tăiere cu laserșiTăiere cu plasmăMai jos este o analiză detaliată și o explicație suplimentară a acestor trei tehnici:
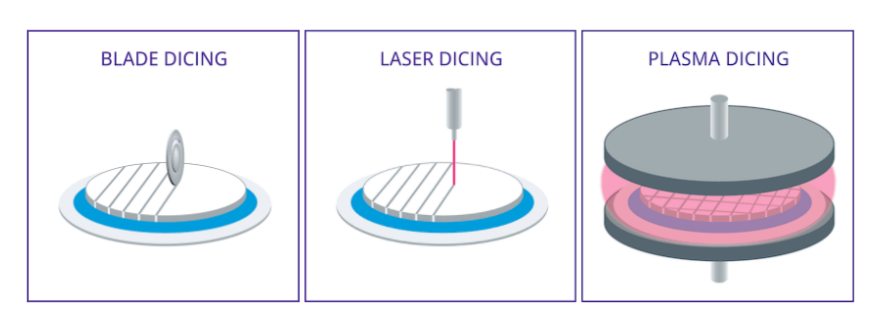
În fabricarea semiconductorilor, tăierea plachetelor este o etapă crucială care necesită selectarea metodei de tăiere adecvate în funcție de grosimea plachetei. Primul pas este determinarea grosimii plachetei. Dacă grosimea plachetei depășește 100 microni, se poate alege tăierea cu lamele ca metodă de tăiere. Dacă tăierea cu lamele nu este potrivită, se poate utiliza metoda de tăiere prin fractură, care include atât tehnici de tăiere prin trasare, cât și tehnici de tăiere cu lamele.
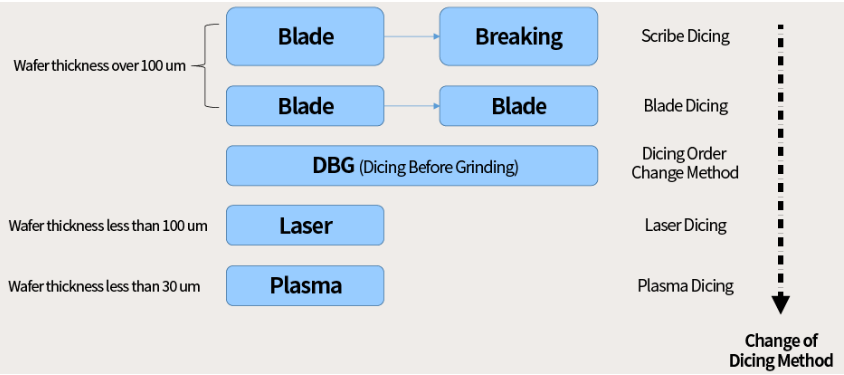
Când grosimea plachetei este între 30 și 100 microni, se recomandă metoda DBG (Dice Before Grinding - Tăiere cu bile înainte de șlefuire). În acest caz, se poate alege tăierea prin trasare, tăierea cu lamă sau ajustarea secvenței de tăiere, după cum este necesar, pentru a obține cele mai bune rezultate.
Pentru napolitane ultra-subțiri cu o grosime mai mică de 30 microni, tăierea cu laser devine metoda preferată datorită capacității sale de a tăia napolitane subțiri cu precizie, fără a provoca daune excesive. Dacă tăierea cu laser nu poate îndeplini cerințele specifice, tăierea cu plasmă poate fi utilizată ca alternativă. Această diagramă de flux oferă o cale clară de luare a deciziilor pentru a asigura alegerea celei mai potrivite tehnologii de tăiere a napolitanelor în diferite condiții de grosime.
2.1 Tehnologia de tăiere mecanică
Tehnologia de tăiere mecanică este metoda tradițională în tăierea plachetelor. Principiul de bază este utilizarea unei pietre abrazive diamantate rotative de mare viteză ca unealtă de tăiere pentru a felia placheta. Echipamentul cheie include un ax cu rulment de aer, care acționează unealta pietrei abrazive diamantate la viteze mari pentru a efectua tăieri sau canelarea precisă de-a lungul unei traiectorii de tăiere predefinite. Această tehnologie este utilizată pe scară largă în industrie datorită costului redus, eficienței ridicate și aplicabilității largi.
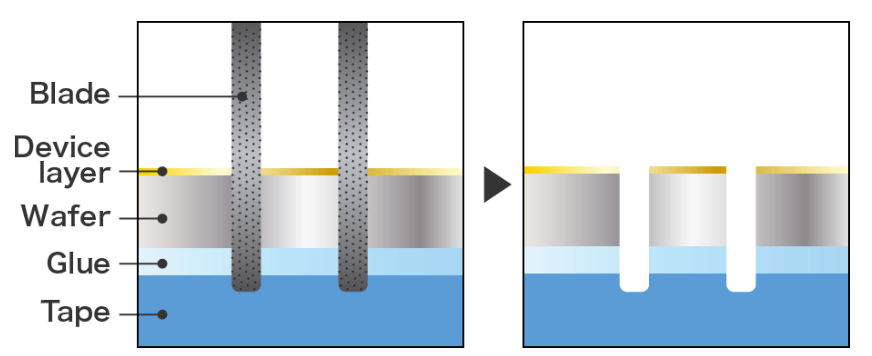
Avantaje
Duritatea ridicată și rezistența la uzură a sculelor abrazive cu diamant permit tehnologiei de tăiere mecanică să se adapteze nevoilor de tăiere a diferitelor materiale pentru napolitane, fie că este vorba de materiale tradiționale pe bază de siliciu sau de semiconductori compuși mai noi. Funcționarea sa este simplă, cu cerințe tehnice relativ scăzute, ceea ce promovează și mai mult popularitatea sa în producția de masă. În plus, în comparație cu alte metode de tăiere, cum ar fi tăierea cu laser, tăierea mecanică are costuri mai controlabile, fiind potrivită pentru nevoile de producție de volum mare.
Limitări
În ciuda numeroaselor sale avantaje, tehnologia de tăiere mecanică are și limitări. În primul rând, din cauza contactului fizic dintre sculă și plachetă, precizia de tăiere este relativ limitată, ceea ce duce adesea la abateri dimensionale care pot afecta acuratețea ambalării și testării ulterioare a cipurilor. În al doilea rând, defecte precum ciobirea și fisurile pot apărea cu ușurință în timpul procesului de tăiere mecanică, ceea ce nu numai că afectează rata de randament, dar poate avea un impact negativ și asupra fiabilității și duratei de viață a cipurilor. Deteriorarea indusă de stresul mecanic este deosebit de dăunătoare pentru fabricarea cipurilor de mare densitate, în special la tăierea materialelor fragile, unde aceste probleme sunt mai proeminente.
Îmbunătățiri tehnologice
Pentru a depăși aceste limitări, cercetătorii optimizează continuu procesul de așchiere mecanică. Îmbunătățirile cheie includ optimizarea designului și a selecției materialelor corpurilor de șlefuit pentru a îmbunătăți precizia și durabilitatea așchierii. În plus, optimizarea designului structural și a sistemelor de control ale echipamentelor de așchiere a îmbunătățit și mai mult stabilitatea și automatizarea procesului de așchiere. Aceste progrese reduc erorile cauzate de operațiunile umane și îmbunătățesc consecvența așchierilor. Introducerea tehnologiilor avansate de inspecție și control al calității pentru monitorizarea în timp real a anomaliilor în timpul procesului de așchiere a îmbunătățit, de asemenea, semnificativ fiabilitatea și randamentul așchierii.
Dezvoltare viitoare și noi tehnologii
Deși tehnologia de tăiere mecanică încă ocupă o poziție semnificativă în tăierea plachetelor, noile tehnologii de tăiere avansează rapid pe măsură ce procesele semiconductorilor evoluează. De exemplu, aplicarea tehnologiei de tăiere termică cu laser oferă noi soluții pentru problemele de precizie și defecte în tăierea mecanică. Această metodă de tăiere fără contact reduce stresul fizic asupra plachetei, reducând semnificativ incidența ciobirii și fisurării, în special la tăierea materialelor mai fragile. În viitor, integrarea tehnologiei de tăiere mecanică cu tehnicile emergente de tăiere va oferi producției de semiconductori mai multe opțiuni și flexibilitate, sporind și mai mult eficiența fabricației și calitatea cipurilor.
În concluzie, deși tehnologia de tăiere mecanică prezintă anumite dezavantaje, îmbunătățirile tehnologice continue și integrarea acesteia cu noile tehnici de tăiere îi permit să joace în continuare un rol important în fabricarea semiconductorilor și să își mențină competitivitatea în procesele viitoare.
2.2 Tehnologia de tăiere cu laser
Tehnologia de tăiere cu laser, ca metodă nouă în tăierea plachetelor, a câștigat treptat o atenție largă în industria semiconductorilor datorită preciziei sale ridicate, lipsei de deteriorări mecanice prin contact și capacităților rapide de tăiere. Această tehnologie utilizează densitatea mare de energie și capacitatea de focalizare a unui fascicul laser pentru a crea o mică zonă afectată termic pe suprafața materialului plachetei. Atunci când fasciculul laser este aplicat pe plachetă, stresul termic generat determină fracturarea materialului în locația desemnată, realizând o tăiere precisă.
Avantajele tehnologiei de tăiere cu laser
• Precizie ridicatăCapacitatea de poziționare precisă a fasciculului laser permite o precizie de tăiere la nivel de microni sau chiar nanometri, îndeplinind cerințele fabricației moderne de circuite integrate de înaltă precizie și densitate mare.
• Fără contact mecanicTăierea cu laser evită contactul fizic cu placheta, prevenind problemele comune în tăierea mecanică, cum ar fi ciobirea și crăparea, îmbunătățind semnificativ rata de randament și fiabilitatea cipurilor.
• Viteză mare de tăiereViteza mare a tăierii cu laser contribuie la creșterea eficienței producției, fiind deosebit de potrivită pentru scenarii de producție la scară largă și de mare viteză.
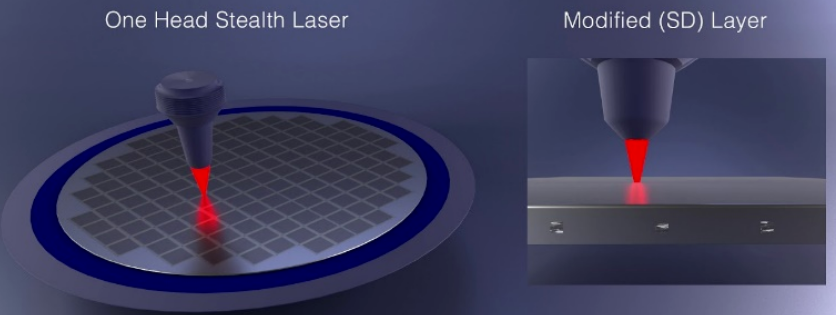
Provocări întâmpinate
• Cost ridicat al echipamentelorInvestiția inițială în echipamentele de tăiere cu laser este mare, ceea ce reprezintă o presiune economică, în special pentru întreprinderile de producție mici și mijlocii.
• Controlul complex al proceselorTăierea cu laser necesită un control precis al mai multor parametri, inclusiv densitatea energiei, poziția focalizării și viteza de tăiere, ceea ce face ca procesul să fie complex.
• Probleme ale zonei afectate de căldurăDeși natura fără contact a tăierii cu laser reduce daunele mecanice, stresul termic cauzat de zona afectată termic (HAZ) poate avea un impact negativ asupra proprietăților materialului napolitan. Este necesară o optimizare suplimentară a procesului pentru a minimiza acest efect.
Direcții de îmbunătățire tehnologică
Pentru a aborda aceste provocări, cercetătorii se concentrează pe reducerea costurilor echipamentelor, îmbunătățirea eficienței tăierii și optimizarea fluxului de proces.
• Lasere și sisteme optice eficientePrin dezvoltarea unor lasere mai eficiente și a unor sisteme optice avansate, este posibil să se reducă costurile echipamentelor, sporind în același timp precizia și viteza de tăiere.
• Optimizarea parametrilor de procesSe desfășoară cercetări aprofundate privind interacțiunea dintre lasere și materialele pentru plachete pentru a îmbunătăți procesele care reduc zona afectată termic, îmbunătățind astfel calitatea tăierii.
• Sisteme inteligente de controlDezvoltarea tehnologiilor inteligente de control are ca scop automatizarea și optimizarea procesului de tăiere cu laser, îmbunătățind stabilitatea și consecvența acestuia.
Tehnologia de tăiere cu laser este deosebit de eficientă în cazul napolitanelor ultra-subțiri și al scenariilor de tăiere de înaltă precizie. Pe măsură ce dimensiunile napolitanelor și densitățile circuitelor cresc, metodele tradiționale de tăiere mecanică se luptă să îndeplinească cerințele de înaltă precizie și eficiență ridicată ale fabricării moderne de semiconductori. Datorită avantajelor sale unice, tăierea cu laser devine soluția preferată în aceste domenii.
Deși tehnologia de tăiere cu laser se confruntă în continuare cu provocări precum costurile ridicate ale echipamentelor și complexitatea procesului, avantajele sale unice în ceea ce privește precizia ridicată și deteriorarea fără contact o fac o direcție importantă de dezvoltare în fabricarea semiconductorilor. Pe măsură ce tehnologia laser și sistemele inteligente de control continuă să avanseze, se așteaptă ca tăierea cu laser să îmbunătățească și mai mult eficiența și calitatea tăierii plachetelor, stimulând dezvoltarea continuă a industriei semiconductorilor.
2.3 Tehnologia de tăiere cu plasmă
Tehnologia de tăiere cu plasmă, ca metodă emergentă de tăiere a napolitanelor, a câștigat o atenție semnificativă în ultimii ani. Această tehnologie utilizează fascicule de plasmă de înaltă energie pentru a tăia cu precizie napolitanele prin controlul energiei, vitezei și traiectoriei de tăiere a fasciculului de plasmă, obținând rezultate optime de tăiere.
Principiul de funcționare și avantajele
Procesul de tăiere cu plasmă se bazează pe un fascicul de plasmă la temperatură înaltă și energie mare, generat de echipament. Acest fascicul poate încălzi materialul napolitan până la punctul său de topire sau vaporizare într-un timp foarte scurt, permițând tăierea rapidă. Comparativ cu tăierea mecanică tradițională sau cu laser, tăierea cu plasmă este mai rapidă și produce o zonă mai mică afectată termic, reducând eficient apariția fisurilor și a deteriorării în timpul tăierii.
În aplicațiile practice, tehnologia de tăiere cu plasmă este deosebit de abilă pentru manipularea napolitanelor cu forme complexe. Fasciculul său de plasmă reglabil, de înaltă energie, poate tăia cu ușurință napolitane de forme neregulate cu o precizie ridicată. Prin urmare, în fabricarea microelectronică, în special în producția personalizată și în loturi mici de cipuri de înaltă performanță, această tehnologie promite o utilizare pe scară largă.
Provocări și limitări
În ciuda numeroaselor avantaje ale tehnologiei de tăiere cu plasmă, aceasta se confruntă și cu unele provocări.
• Proces complexProcesul de tăiere cu plasmă este complex și necesită echipamente de înaltă precizie și operatori experimentați pentru a asiguraprecizie și stabilitate la tăiere.
• Controlul și siguranța mediuluiNatura la temperatură înaltă și energie ridicată a fasciculului de plasmă necesită măsuri stricte de control al mediului și de siguranță, ceea ce crește complexitatea și costul implementării.
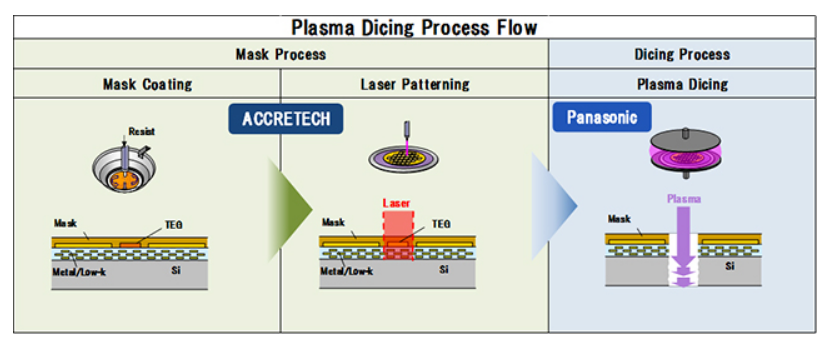
Direcții de dezvoltare viitoare
Odată cu progresele tehnologice, se așteaptă ca provocările asociate cu tăierea cu plasmă să fie depășite treptat. Prin dezvoltarea unor echipamente de tăiere mai inteligente și mai stabile, se poate reduce dependența de operațiunile manuale, îmbunătățind astfel eficiența producției. În același timp, optimizarea parametrilor procesului și a mediului de tăiere va contribui la reducerea riscurilor de siguranță și a costurilor operaționale.
În industria semiconductorilor, inovațiile în tehnologia de tăiere și debitare a napolitanelor sunt cruciale pentru dezvoltarea industriei. Tehnologia de tăiere cu plasmă, cu precizia, eficiența și capacitatea sa ridicată de a gestiona forme complexe de napolitane, a apărut ca un nou jucător important în acest domeniu. Deși rămân unele provocări, aceste probleme vor fi abordate treptat prin inovații tehnologice continue, aducând mai multe posibilități și oportunități în fabricarea semiconductorilor.
Perspectivele de aplicare ale tehnologiei de tăiere cu plasmă sunt vaste și se așteaptă ca aceasta să joace un rol mai important în fabricarea semiconductorilor în viitor. Prin inovație tehnologică și optimizare continuă, tăierea cu plasmă nu numai că va aborda provocările existente, dar va deveni și un factor puternic al creșterii industriei semiconductorilor.
2.4 Calitatea tăierii și factorii care o influențează
Calitatea tăierii napolitane este esențială pentru ambalarea ulterioară a cipurilor, testarea și performanța și fiabilitatea generală a produsului final. Problemele frecvente întâlnite în timpul tăierii includ fisuri, ciobiri și abateri de la tăiere. Aceste probleme sunt influențate de mai mulți factori care interacționează.
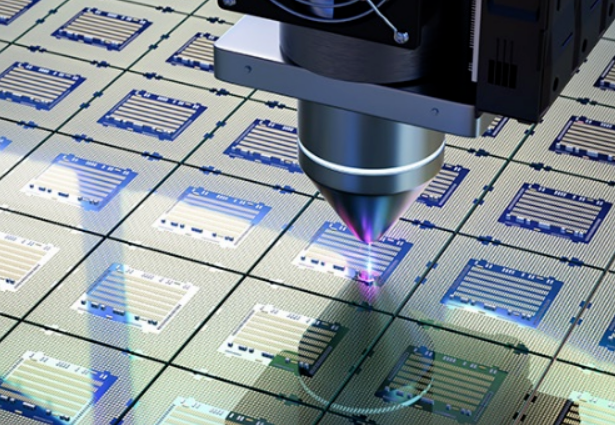
Categorie | Conţinut | Impact |
Parametrii procesului | Viteza de tăiere, avansul și adâncimea de tăiere afectează direct stabilitatea și precizia procesului de tăiere. Setările necorespunzătoare pot duce la concentrarea stresului și la o zonă afectată termic excesiv, rezultând fisuri și ciobiri. Ajustarea parametrilor în mod corespunzător, în funcție de materialul plachetei, grosime și cerințele de tăiere, este esențială pentru obținerea rezultatelor dorite. | Parametrii de proces corecți asigură o tăiere precisă și reduc riscul de defecte precum fisuri și ciobiri. |
Factori de echipamente și materiale | -Calitatea lameiMaterialul, duritatea și rezistența la uzură a lamei influențează netezimea procesului de tăiere și planeitatea suprafeței tăiate. Lamele de calitate slabă cresc frecarea și stresul termic, putând duce la fisuri sau ciobire. Alegerea materialului potrivit pentru lamă este crucială. -Performanța lichidului de răcireLichidele de răcire ajută la reducerea temperaturii de tăiere, la minimizarea frecării și la îndepărtarea resturilor. Lichidul de răcire ineficient poate duce la temperaturi ridicate și la acumularea de resturi, afectând calitatea și eficiența tăierii. Selectarea unor lichide de răcire eficiente și ecologice este vitală. | Calitatea lamei afectează precizia și netezimea tăierii. Lichidul de răcire ineficient poate duce la o calitate și o eficiență slabă a tăierii, subliniind necesitatea utilizării optime a lichidului de răcire. |
Controlul proceselor și inspecția calității | -Controlul proceselorMonitorizare și ajustare în timp real a parametrilor cheie de tăiere pentru a asigura stabilitatea și consecvența procesului de tăiere. -Inspecția calitățiiVerificările aspectului post-tăiere, măsurătorile dimensionale și testarea performanței electrice ajută la identificarea și remedierea promptă a problemelor de calitate, îmbunătățind precizia și consecvența tăierii. | Controlul adecvat al procesului și inspecția calității ajută la asigurarea unor rezultate de tăiere consistente și de înaltă calitate, precum și la detectarea timpurie a potențialelor probleme. |

Îmbunătățirea calității tăierii
Îmbunătățirea calității tăierii necesită o abordare cuprinzătoare care să ia în considerare parametrii procesului, selecția echipamentelor și materialelor, controlul și inspecția procesului. Prin rafinarea continuă a tehnologiilor de tăiere și optimizarea metodelor de proces, precizia și stabilitatea tăierii plachetelor pot fi îmbunătățite în continuare, oferind un suport tehnic mai fiabil pentru industria de fabricație a semiconductorilor.
#03 Manipularea și testarea post-tăiere
3.1 Curățare și uscare
Etapele de curățare și uscare după tăierea plachetelor sunt esențiale pentru asigurarea calității cipurilor și a progresiei line a proceselor ulterioare. În această etapă, este esențial să se îndepărteze complet resturile de siliciu, reziduurile de lichid de răcire și alți contaminanți generați în timpul tăierii. Este la fel de important să se asigure că cipurile nu sunt deteriorate în timpul procesului de curățare și, după uscare, să se asigure că nu rămâne umiditate pe suprafața cipurilor pentru a preveni probleme precum coroziunea sau descărcarea electrostatică.
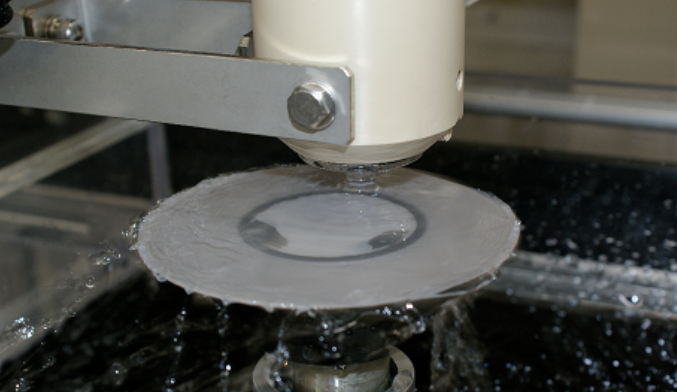
Manipularea post-tăiere: Procesul de curățare și uscare
Etapa procesului | Conţinut | Impact |
Procesul de curățare | -MetodăFolosiți agenți de curățare specializați și apă pură, combinați cu tehnici de periere cu ultrasunete sau mecanică pentru curățare. | Asigură îndepărtarea completă a contaminanților și previne deteriorarea așchiilor în timpul curățării. |
-Selectarea agentului de curățareAlegeți în funcție de materialul plachetei și de tipul de contaminant pentru a asigura o curățare eficientă fără a deteriora cipul. | Alegerea corectă a agentului este esențială pentru o curățare eficientă și o protecție împotriva așchiilor. | |
-Controlul parametrilorControlați cu strictețe temperatura, timpul și concentrația soluției de curățare pentru a preveni problemele de calitate cauzate de curățarea necorespunzătoare. | Controalele ajută la evitarea deteriorării plachetei sau a lăsării de contaminanți, asigurând o calitate constantă. | |
Procesul de uscare | -Metode tradiționaleUscarea naturală cu aer și uscarea cu aer cald, care au o eficiență scăzută și pot duce la acumularea de electricitate statică. | Poate duce la timpi de uscare mai lenți și la potențiale probleme de electricitate statică. |
-Tehnologii moderneFolosiți tehnologii avansate, cum ar fi uscarea în vid și uscarea cu infraroșu, pentru a vă asigura că așchiile se usucă rapid și pentru a evita efectele nocive. | Proces de uscare mai rapid și mai eficient, reducând riscul de descărcare statică sau probleme legate de umiditate. | |
Selectarea și întreținerea echipamentelor | -Selecția echipamentelorMașinile de curățare și uscare de înaltă performanță îmbunătățesc eficiența procesării și controlează fin potențialele probleme în timpul manipulării. | Mașinile de înaltă calitate asigură o procesare mai bună și reduc probabilitatea erorilor în timpul curățării și uscării. |
-Întreținerea echipamentelorInspecția și întreținerea regulată a echipamentelor asigură menținerea acestora în stare optimă de funcționare, garantând calitatea așchiilor. | Întreținerea adecvată previne defecțiunile echipamentelor, asigurând o procesare fiabilă și de înaltă calitate. |
Curățare și uscare după tăiere
Etapele de curățare și uscare după tăierea plachetelor sunt procese complexe și delicate care necesită o analiză atentă a mai multor factori pentru a asigura rezultatul final al procesării. Prin utilizarea metodelor științifice și a procedurilor riguroase, este posibil să se asigure că fiecare cip intră în etapele ulterioare de ambalare și testare în condiții optime.
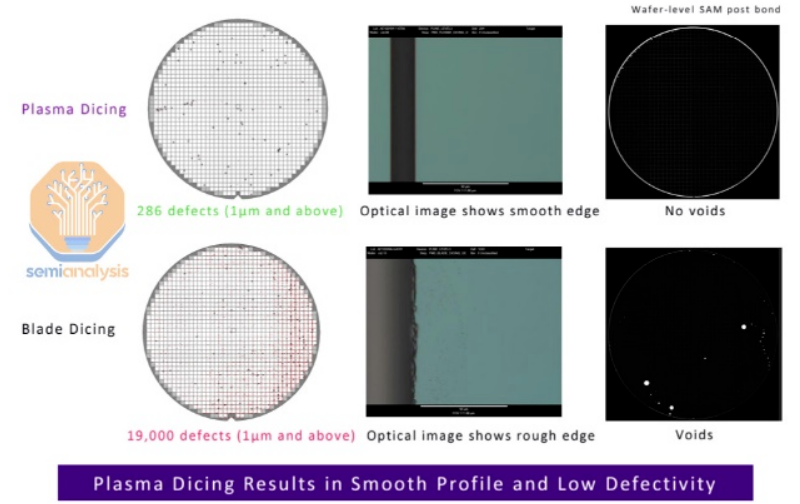
Inspecția și testarea post-tăiere
Pas | Conţinut | Impact |
Etapa de inspecție | 1.Inspecție vizualăFolosiți echipamente de inspecție vizuală sau automată pentru a verifica dacă există defecte vizibile, cum ar fi fisuri, ciobiri sau contaminare pe suprafața așchiilor. Identificați rapid așchiile deteriorate fizic pentru a evita risipa. | Ajută la identificarea și eliminarea așchiilor defecte la începutul procesului, reducând pierderile de material. |
2.Măsurarea dimensiuniiFolosiți dispozitive de măsurare de precizie pentru a măsura cu exactitate dimensiunile cipurilor, asigurându-vă că dimensiunea tăiată respectă specificațiile de proiectare și prevenind problemele de performanță sau dificultățile de ambalare. | Asigură că cipurile se încadrează în limitele de dimensiune necesare, prevenind degradarea performanței sau problemele de asamblare. | |
3.Testarea performanței electriceEvaluați parametrii electrici cheie, cum ar fi rezistența, capacitatea și inductanța, pentru a identifica cipurile neconforme și a vă asigura că doar cipurile calificate din punct de vedere al performanței trec la etapa următoare. | Asigură că doar cipurile funcționale și testate pentru performanță avansează în acest proces, reducând riscul de defecțiune în etapele ulterioare. | |
Etapa de testare | 1.Testarea funcționalăVerificați dacă funcționalitatea de bază a cipului funcționează conform așteptărilor, identificând și eliminând cipurile cu anomalii funcționale. | Se asigură că cipurile îndeplinesc cerințele operaționale de bază înainte de a trece la etapele ulterioare. |
2.Testarea fiabilitățiiEvaluează stabilitatea performanței cipurilor în condiții de utilizare prelungită sau în medii dure, implicând de obicei îmbătrânirea la temperaturi ridicate, testarea la temperaturi scăzute și testarea umidității pentru a simula condiții extreme din lumea reală. | Asigură funcționarea fiabilă a cipurilor într-o gamă largă de condiții de mediu, îmbunătățind longevitatea și stabilitatea produsului. | |
3.Testarea compatibilitățiiVerificați dacă cipul funcționează corect cu alte componente sau sisteme, asigurându-vă că nu există erori sau degradări ale performanței din cauza incompatibilității. | Asigură funcționarea fără probleme în aplicațiile din lumea reală, prevenind problemele de compatibilitate. |
3.3 Ambalare și depozitare
După tăierea plachetelor, cipurile reprezintă un rezultat crucial al procesului de fabricație a semiconductorilor, iar etapele de ambalare și depozitare a acestora sunt la fel de importante. Măsurile adecvate de ambalare și depozitare sunt esențiale nu numai pentru asigurarea siguranței și stabilității cipurilor în timpul transportului și depozitării, ci și pentru a oferi un suport solid pentru etapele ulterioare de producție, testare și ambalare.
Rezumatul etapelor de inspecție și testare:
Etapele de inspecție și testare a cipurilor după tăierea plachetelor acoperă o gamă largă de aspecte, inclusiv inspecția vizuală, măsurarea dimensiunilor, testarea performanței electrice, testarea funcțională, testarea fiabilității și testarea compatibilității. Aceste etape sunt interconectate și complementare, formând o barieră solidă pentru a asigura calitatea și fiabilitatea produsului. Prin proceduri stricte de inspecție și testare, problemele potențiale pot fi identificate și rezolvate prompt, asigurându-se că produsul final îndeplinește cerințele și așteptările clienților.
Aspect | Conţinut |
Măsuri de ambalare | 1.AntistaticMaterialele de ambalare trebuie să aibă proprietăți antistatice excelente pentru a preveni deteriorarea dispozitivelor sau afectarea performanței acestora de către electricitatea statică. |
2.Rezistent la umiditateMaterialele de ambalare trebuie să aibă o bună rezistență la umiditate pentru a preveni coroziunea și deteriorarea performanței electrice cauzate de umiditate. | |
3.Rezistent la șocuriMaterialele de ambalare trebuie să ofere o absorbție eficientă a șocurilor pentru a proteja așchiile de vibrații și impact în timpul transportului. | |
Mediul de depozitare | 1.Controlul umiditățiiControlați cu strictețe umiditatea într-un interval adecvat pentru a preveni absorbția umezelii și coroziunea cauzate de umiditatea excesivă sau problemele statice cauzate de umiditatea scăzută. |
2.CurăţenieMențineți un mediu de depozitare curat pentru a evita contaminarea așchiilor cu praf și impurități. | |
3.Controlul temperaturiiSetați un interval de temperatură rezonabil și mențineți stabilitatea temperaturii pentru a preveni îmbătrânirea accelerată din cauza căldurii excesive sau a problemelor de condens cauzate de temperaturile scăzute. | |
Inspecție regulată | Inspectați și evaluați periodic cipurile depozitate, utilizând inspecții vizuale, măsurători ale dimensiunilor și teste de performanță electrică pentru a identifica și remedia potențialele probleme în timp util. Pe baza timpului și condițiilor de depozitare, planificați utilizarea cipurilor pentru a vă asigura că acestea sunt utilizate în condiții optime. |
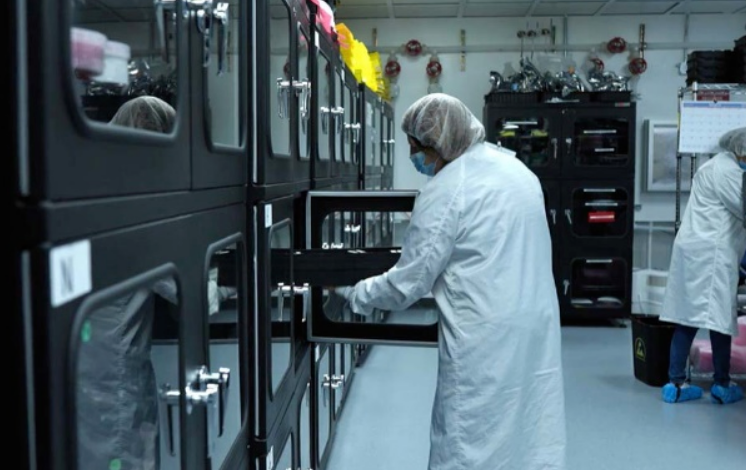
Problema microfisurilor și a deteriorării în timpul procesului de tăiere a napolitanelor reprezintă o provocare semnificativă în fabricarea semiconductorilor. Stresul de tăiere este cauza principală a acestui fenomen, deoarece creează fisuri minuscule și deteriorări pe suprafața napolitanei, ceea ce duce la creșterea costurilor de fabricație și la scăderea calității produsului.
Pentru a aborda această provocare, este crucial să se minimizeze stresul de tăiere și să se implementeze tehnici, unelte și condiții de tăiere optimizate. O atenție deosebită la factori precum materialul lamei, viteza de tăiere, presiunea și metodele de răcire poate ajuta la reducerea formării microfisurilor și la îmbunătățirea randamentului general al procesului. În plus, cercetările continue privind tehnologiile de tăiere mai avansate, cum ar fi tăierea cu laser, explorează modalități de atenuare a acestor probleme.
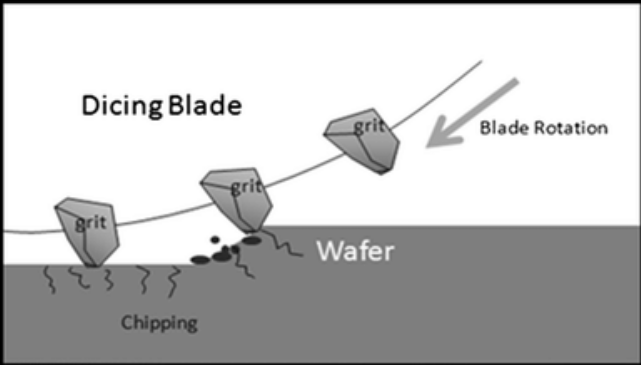
Fiind un material fragil, napolitanele sunt predispuse la modificări structurale interne atunci când sunt supuse unor solicitări mecanice, termice sau chimice, ceea ce duce la formarea de microfisuri. Deși aceste fisuri pot să nu fie imediat observabile, ele se pot extinde și pot provoca daune mai grave pe măsură ce procesul de fabricație progresează. Această problemă devine deosebit de dificilă în timpul etapelor ulterioare de ambalare și testare, unde fluctuațiile de temperatură și solicitările mecanice suplimentare pot determina ca aceste microfisuri să evolueze în fracturi vizibile, ceea ce poate duce la defectarea cipului.
Pentru a atenua acest risc, este esențial să se controleze cu atenție procesul de tăiere prin optimizarea parametrilor precum viteza de tăiere, presiunea și temperatura. Utilizarea unor metode de tăiere mai puțin agresive, cum ar fi tăierea cu laser, poate reduce stresul mecanic asupra plachetei și poate minimiza formarea microfisurilor. În plus, implementarea unor metode avansate de inspecție, cum ar fi scanarea în infraroșu sau imagistica cu raze X, în timpul procesului de tăiere a plachetei, poate ajuta la detectarea acestor fisuri în stadiu incipient înainte ca acestea să provoace daune suplimentare.
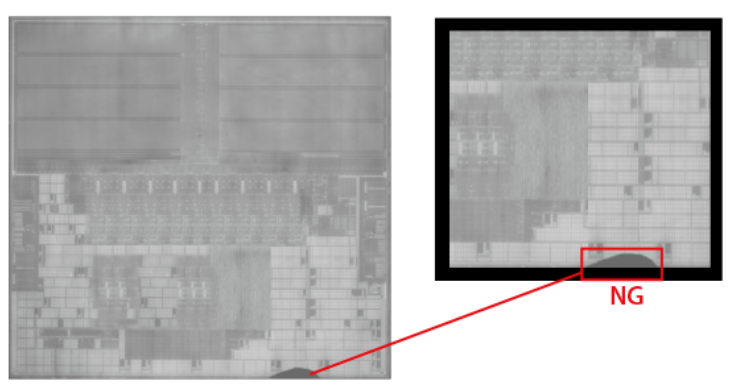
Deteriorarea suprafeței plachetei reprezintă o preocupare semnificativă în procesul de tăiere în cuburi, deoarece poate avea un impact direct asupra performanței și fiabilității cipului. Astfel de daune pot fi cauzate de utilizarea necorespunzătoare a sculelor de tăiere, parametri de tăiere incorecți sau defecte de material inerente plachetei în sine. Indiferent de cauză, aceste daune pot duce la modificări ale rezistenței electrice sau capacității circuitului, afectând performanța generală.
Pentru a aborda aceste probleme, se explorează două strategii cheie:
1. Optimizarea sculelor așchietoare și a parametrilorPrin utilizarea unor lame mai ascuțite, reglarea vitezei de tăiere și modificarea adâncimii de tăiere, concentrarea stresului în timpul procesului de tăiere poate fi redusă la minimum, reducând astfel potențialul de deteriorare.
2. Explorarea noilor tehnologii de tăiereTehnicile avansate precum tăierea cu laser și tăierea cu plasmă oferă o precizie îmbunătățită, reducând în același timp nivelul de deteriorare a plăcii. Aceste tehnologii sunt studiate pentru a găsi modalități de a obține o precizie ridicată a tăierii, reducând în același timp stresul termic și mecanic asupra plăcii.
Zona de impact termic și efectele acesteia asupra performanței
În procesele de tăiere termică, cum ar fi tăierea cu laser și cu plasmă, temperaturile ridicate creează inevitabil o zonă de impact termic pe suprafața plachetei. Această zonă, unde gradientul de temperatură este semnificativ, poate altera proprietățile materialului, afectând performanța finală a cipului.
Impactul Zonei Afectate Termic (TAZ):
Modificări ale structurii cristalineLa temperaturi ridicate, atomii din materialul plachetei se pot rearanja, provocând distorsiuni ale structurii cristaline. Această distorsiune slăbește materialul, reducându-i rezistența mecanică și stabilitatea, ceea ce crește riscul de defecțiune a cipului în timpul utilizării.
Modificări ale proprietăților electriceTemperaturile ridicate pot modifica concentrația și mobilitatea purtătorilor de curent în materialele semiconductoare, afectând conductivitatea electrică și eficiența transmisiei curentului cipului. Aceste modificări pot duce la o scădere a performanței cipului, făcându-l potențial impropriu scopului propus.
Pentru a atenua aceste efecte, controlul temperaturii în timpul tăierii, optimizarea parametrilor de tăiere și explorarea unor metode precum jeturile de răcire sau tratamentele post-procesare sunt strategii esențiale pentru a reduce amploarea impactului termic și a menține integritatea materialului.
Per ansamblu, atât microfisurile, cât și zonele de impact termic reprezintă provocări cruciale în tehnologia de tăiere a napolitanelor. Cercetările continue, alături de progresele tehnologice și măsurile de control al calității, vor fi necesare pentru a îmbunătăți calitatea produselor semiconductoare și a spori competitivitatea acestora pe piață.
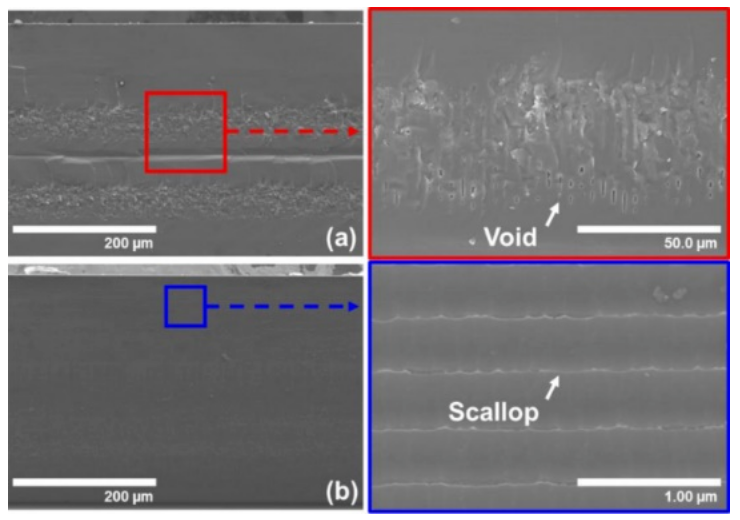
Măsuri pentru controlul zonei de impact termic:
Optimizarea parametrilor procesului de tăiereReducerea vitezei și a puterii de tăiere poate reduce eficient dimensiunea zonei de impact termic (TAZ). Acest lucru ajută la controlul cantității de căldură generate în timpul procesului de tăiere, care are un impact direct asupra proprietăților materialului plachetei.
Tehnologii avansate de răcireAplicarea unor tehnologii precum răcirea cu azot lichid și răcirea microfluidică poate limita semnificativ raza de acțiune a zonei de impact termic. Aceste metode de răcire ajută la disiparea mai eficientă a căldurii, păstrând astfel proprietățile materialului plachetei și minimizând daunele termice.
Selecția materialelorCercetătorii explorează materiale noi, cum ar fi nanotuburile de carbon și grafenul, care posedă o conductivitate termică și o rezistență mecanică excelente. Aceste materiale pot reduce zona de impact termic, îmbunătățind în același timp performanța generală a cipurilor.
În concluzie, deși zona de impact termic este o consecință inevitabilă a tehnologiilor de tăiere termică, aceasta poate fi controlată eficient prin tehnici de procesare optimizate și selecție a materialelor. Cercetările viitoare se vor concentra probabil pe reglarea fină și automatizarea proceselor de tăiere termică pentru a obține o tăiere mai eficientă și mai precisă a napolitanelor.

Strategia de echilibru:
Atingerea echilibrului optim între randamentul napolitanelor și eficiența producției este o provocare continuă în tehnologia de tăiere a napolitanelor. Producătorii trebuie să ia în considerare mai mulți factori, cum ar fi cererea pieței, costurile de producție și calitatea produsului, pentru a dezvolta o strategie de producție rațională și parametrii de proces. În același timp, introducerea echipamentelor avansate de tăiere, îmbunătățirea abilităților operatorilor și sporirea controlului calității materiilor prime sunt esențiale pentru menținerea sau chiar îmbunătățirea randamentului, crescând în același timp eficiența producției.
Provocări și oportunități viitoare:
Odată cu avansarea tehnologiei semiconductorilor, tăierea plachetelor se confruntă cu noi provocări și oportunități. Pe măsură ce dimensiunile cipurilor se micșorează și integrarea crește, cerințele privind precizia și calitatea tăierii cresc semnificativ. Simultan, tehnologiile emergente oferă noi idei pentru dezvoltarea tehnicilor de tăiere a plachetelor. Producătorii trebuie să rămână la curent cu dinamica pieței și tendințele tehnologice, ajustând și optimizând continuu strategiile de producție și parametrii procesului pentru a satisface schimbările pieței și cerințele tehnologice.
În concluzie, prin integrarea considerațiilor privind cererea pieței, costurile de producție și calitatea produsului, precum și prin introducerea de echipamente și tehnologii avansate, îmbunătățirea abilităților operatorilor și consolidarea controlului materiilor prime, producătorii pot obține cel mai bun echilibru între randamentul napolitanelor și eficiența producției în timpul tăierii napolitanelor, ceea ce duce la o producție eficientă și de înaltă calitate a produselor semiconductoare.
Perspective de viitor:
Odată cu progresele tehnologice rapide, tehnologia semiconductorilor progresează într-un ritm fără precedent. Fiind un pas critic în fabricarea semiconductorilor, tehnologia de tăiere a napolitanelor este pregătită pentru noi dezvoltări interesante. Privind în perspectivă, se așteaptă ca tehnologia de tăiere a napolitanelor să realizeze îmbunătățiri semnificative în ceea ce privește precizia, eficiența și costul, injectând o nouă vitalitate în creșterea continuă a industriei semiconductorilor.
Creșterea preciziei:
În căutarea unei precizii superioare, tehnologia de tăiere a plachetelor va împinge continuu limitele proceselor existente. Prin studierea aprofundată a mecanismelor fizice și chimice ale procesului de tăiere și controlul precis al parametrilor de tăiere, se vor obține rezultate de tăiere mai fine pentru a satisface cerințele de proiectare a circuitelor din ce în ce mai complexe. În plus, explorarea de noi materiale și metode de tăiere va îmbunătăți semnificativ randamentul și calitatea.
Îmbunătățirea eficienței:
Noile echipamente de tăiere a plachetelor se vor concentra pe designul inteligent și automatizat. Introducerea unor sisteme avansate de control și a unor algoritmi va permite echipamentelor să ajusteze automat parametrii de tăiere pentru a se adapta diferitelor materiale și cerințe de design, îmbunătățind astfel semnificativ eficiența producției. Inovații precum tehnologia de tăiere cu plachete multiple și sistemele de înlocuire rapidă a lamelor vor juca un rol crucial în creșterea eficienței.
Reducerea costurilor:
Reducerea costurilor este o direcție cheie pentru dezvoltarea tehnologiei de tăiere a plachetelor. Pe măsură ce sunt dezvoltate noi materiale și metode de tăiere, se așteaptă ca costurile echipamentelor și cheltuielile de întreținere să fie controlate eficient. În plus, optimizarea proceselor de producție și reducerea ratelor de rebut vor reduce și mai mult deșeurile în timpul fabricației, ceea ce va duce la o scădere a costurilor generale de producție.
Fabricație inteligentă și IoT:
Integrarea tehnologiilor de fabricație inteligentă și a internetului obiectelor (IoT) va aduce schimbări transformatoare în tehnologia de tăiere a plachetelor. Prin interconectivitate și partajarea datelor între dispozitive, fiecare etapă a procesului de producție poate fi monitorizată și optimizată în timp real. Acest lucru nu numai că îmbunătățește eficiența producției și calitatea produsului, dar oferă și companiilor previziuni de piață și suport decizional mai precise.
În viitor, tehnologia de tăiere a plachetelor va face progrese remarcabile în ceea ce privește precizia, eficiența și costul. Aceste progrese vor impulsiona dezvoltarea continuă a industriei semiconductorilor și vor aduce mai multe inovații tehnologice și facilități societății umane.
Data publicării: 19 noiembrie 2024